PRODUCT
صفحة رئيسية>منتجات>
استجواب
عندما تلقينا استفسارك ، ونحن سوف نرسل لك كتالوج مخصص ، وقائمة الأسعار ، والتسليم ، وشروط الدفع وغيرها من التفاصيل المطلوبة عن طريق البريد الإلكتروني خلال
cgm ball mill for iron ore fines details for pellet plant
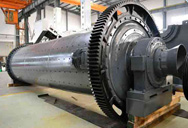
Influence of beneficiation plant pellet grade iron ore fines size on ...
Beneficiation plant product size (pellet grade fines) is coarser (-45micron - 40 to 45%) in nature. Optimum particle size of the raw material is required to get the desired properties 2018年7月11日 Pellets are balls formed by rolling moist concentrates and fines iron ores of different mineral- ogical and chemical composition, with (PDF) Iron Ore Pelletizing Process: An Overview2024年4月22日 This experimental investigation summarized the utilization of (LGIO) fines containing goethite to obtain high-grade iron ore pellets where the waste fines were Reduction Roasting Followed by Pelletization Study of
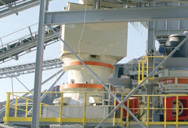
Development of a Novel Grinding Process to Iron Ore Pelletizing
Modern iron ore pelletizing process operations may be divid-ed into two main process sections: feedstock preparation and agglomeration processes. In most plants, the 2022年3月19日 An iron ore concentrate sample was ground separately in a pilot-scale HPGR mill in multiple passes and a dry open-circuit ball mill to increase the specific Grinding iron ore concentrate by using HPGR and ball mills and 2013年7月18日 Pellet plant (42 MPta capacity) of JSW Steel Ltd imports iron ore fines from different mines to produce pellets for its Corex and Blast Furnace plants. The Influence of raw material particle size on quality of pellets
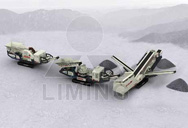
Iron ore pelletization - ScienceDirect
2015年1月1日 Usually wet ball milling is suitable for pretreating magnetite concentrates, while dry ball milling is better for hematite concentrates because finely ground hematite Our iron ore pelletizing systems combine the best features of both technologies to provide the most modern plant and to produce pellets at the lowest cost and highest quality. Iron ore pelletizing - Metso
- beneficiation method of iron ore cost crusher screen plate
- إبرة محطم الكهربائية 500
- عمل محطة معالجة الفحم
- قائمة أسعار كسارة quarstone
- الحديد تخطيط خام مصنع بيليه
- الجرانيت مصنع الرمال الصخرية
- كيف cs محطم العمل
- مطاحن المنشار المحمولة في السعودية
- معدات سوبر فوسفات واحدة تكراشي
- محطم آلة الصانع الجزائر
- أريد شراء كسارة الأسطوانة
- تكلفة الحجر آلة كسارة في صنع الرمال الهند محجر الحجر
- المواصفات 200 الفك محطم
- اسعار غسالة رمل
- iron ore mill manufacturer in china
- صانع معدات البناء في بوال
- حجر التوفا محطم
- تستخدم كسارة الفك في إسرائيل
- صغيرة سحق الحجر المصنعين مصنع مصر
- الموردين الكرة مطحنة طحن